Our way of working differentiates us. It must differentiate us. We know that real estate services and infrastructure are essential. They impact people. They impact our clients’ business.
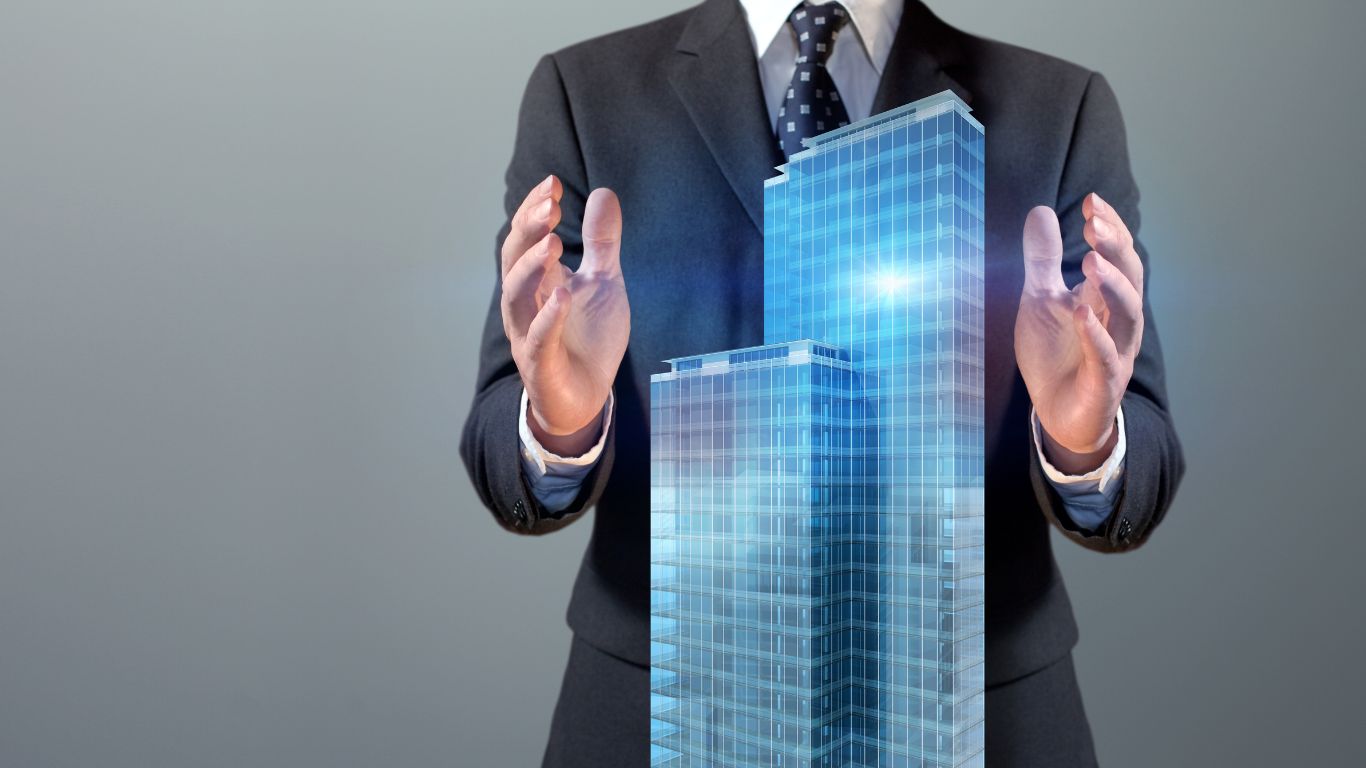
Facility Managment
Innovation and competence in managing a project
The latest addition to the “Sertec house” at the beginning of 2017 is Sertec Facility Management. The key aim is to give continuity to the construction or recovery process of a building, entrusting it, once the testing phase has been completed, into the hands of specialists in the management and operation of systems and services.
The Sertec Facility Management team is made up of specialized technicians – Engineers, Architects, Geologists and Surveyors – who operate transversally on every possible design, maintenance or management topic. High-level professionals who make their know-how available to the customer, coordinating with each other and with installers and maintenance workers to offer a model of excellence in every field.
Know-how
Wide internal sectorisation
Internal professionals
50 specialized technicians
Technological solutions
Target customer needs
Process optimization
NFC TAG technology
Services
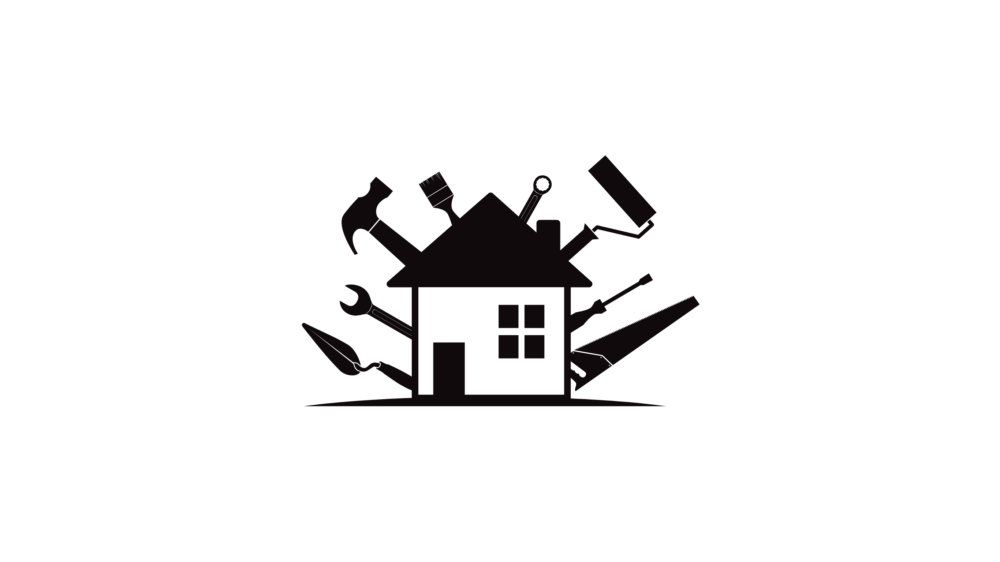
Building services
-
Acquisition and disposal of spaces
-
Project & Engineering
-
“Turnkey” offices
-
User management
-
Energy efficiency
-
BIM methodology
-
General services
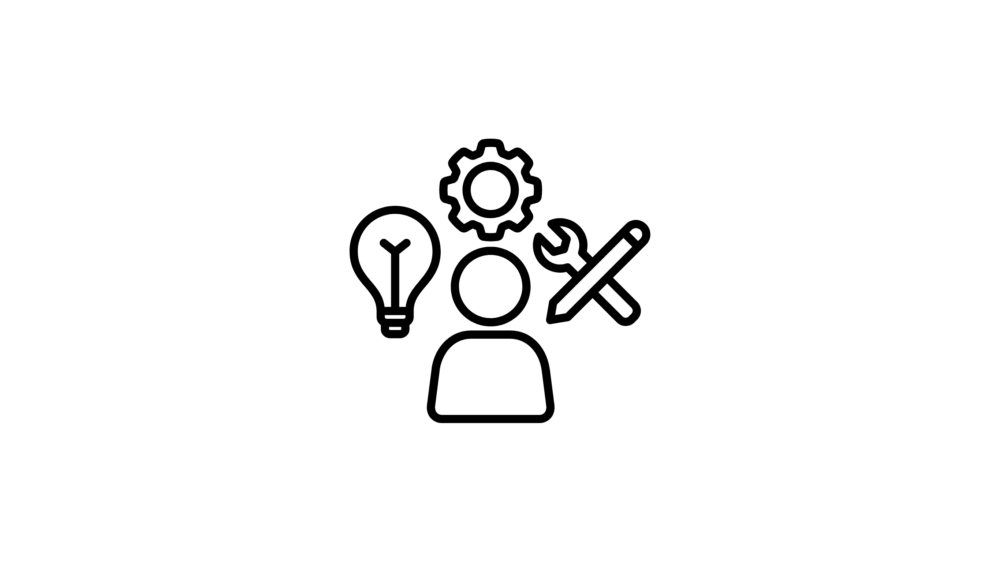
Operation and maintenance of systems
-
Electrical systems
-
Special Plants
-
BMS and home automation systems
-
HVAC systems
-
Plumbing systems
-
Elevator systems
-
Automations
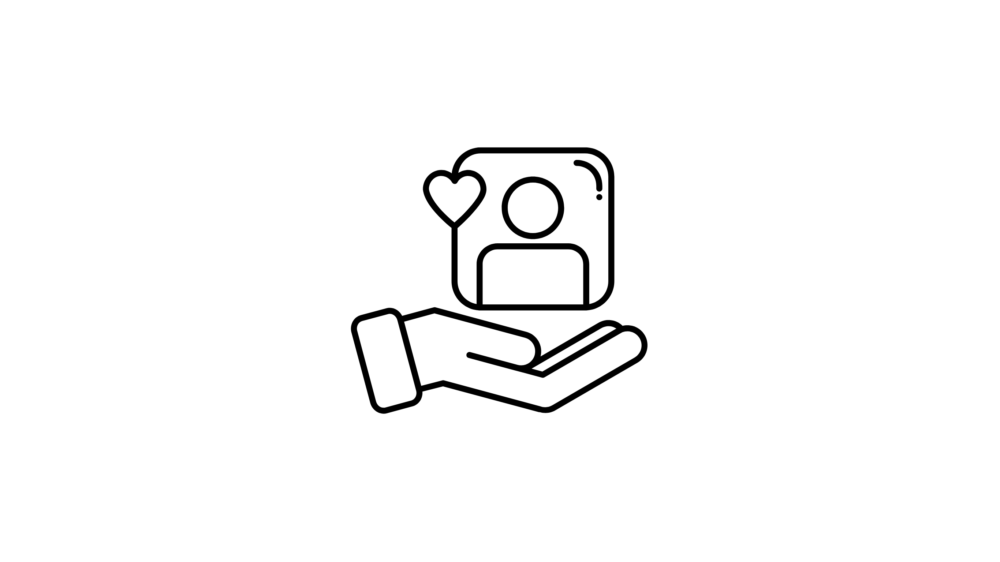
Services to people
-
Document management
-
Cleaning
-
Mail
-
Green activity
-
Catering & cafeteria
-
Guardianship & surveillance
-
Stationery
-
Porterage
-
Car fleet
-
Waste disposal
NFC TAG technology
Control over the supplier is carried out through the use of an innovative management and verification system for ordinary maintenance that SERTEC F.M. developed in close collaboration with a leading Milanese Software House.
The above program is a system that works with NFC technology, which involves the positioning of electronic labels (TAG) on each system managed by the operator – maintenance technician. The TAG interfaces with the Maintenance Operator’s PDA/Smartphone through a dedicated App protected by very rigorous credentials.
For each maintenance intervention or, simply, visual inspection required by the Maintenance Specifications, the Maintenance Engineer is obliged to open the technical/graphic pages associated with the system, examine what is foreseen for that specific intervention, and, following the operations “physical” tests carried out on board the plant, certify the intervention according to a specific, fast procedure.
The data relating to the intervention (start and end times, handwritten certification of the completion of the operation envisaged by the Specifications, any notes, photos and/or comments and/or proposals for improvements or repairs) are immediately transferred to a Data Base managed solely by an external company which prevents the manipulation of the data in any way, guaranteeing its absolute impartiality in the event of a dispute.
The SW processes a large series of easy-to-read reports with performance indicators expressed in a graphic form chosen by the Client (Traffic Light – Graph etc..) so that everything necessary for the correct interpretation of the data can be immediately under control, such as, for example example, delays in carrying out maintenance.
The SW also provides advance notification by e-mail to anyone deemed necessary of the approaching deadline for the next ordinary maintenance intervention on the specific system, sending specific “alerts” or other information.